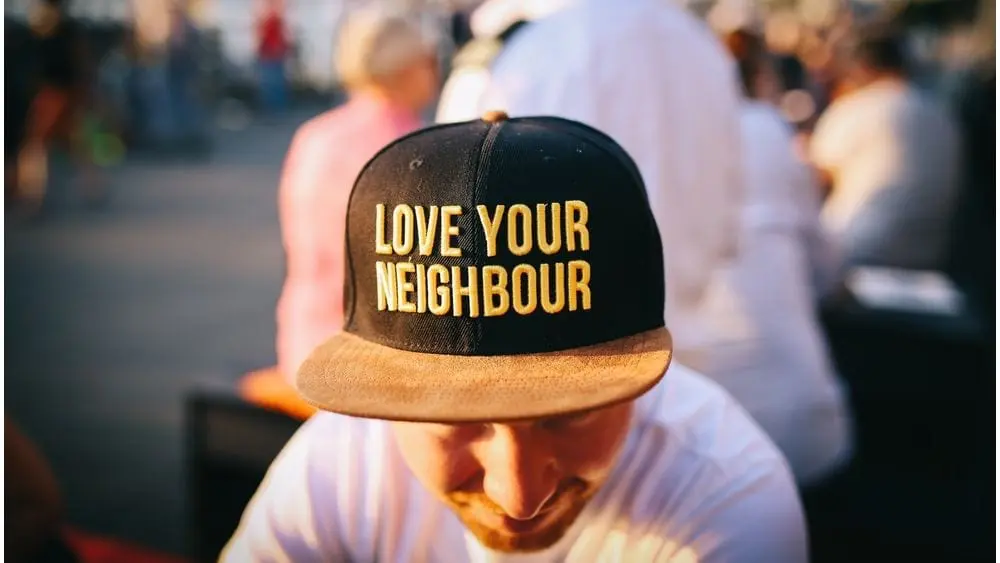
World Vision, the international Christian relief organization, operates storehouses in Appalachia, the Pacific Northwest, Chicagoland, Northern Texas and Greater New York to help families make positive changes in their lives.
The storehouse program has been in existence since 1998; it was started by a group of businessmen in Chicago, who then approached World Vision to take it over, says Larry Noble, World Vision’s national director for corporate engagement. The three areas the storehouses focus on are: essential family supplies, such as clothing, cleaning products and hygiene items; school supplies; and building materials. The storehouses are structured to help World Vision’s local partner organizations lift their communities out of poverty, Noble says.
“Building supplies are such an integral part of that,” he says. “If you don’t have a working toilet or sink or flooring, it doesn’t foster the growth out of poverty that we are seeking.”
Doing Good
Building material and supplies are donated to World Vision’s storehouses to help the organization provide quality building materials to homeowners of modest means. The donated building materials come from national manufacturers, distributors and retailers and are organized into major sectors of supplies — roofing, insulation, windows and doors, flooring and kitchen and bath plumbing, which include sinks, toilets, faucets and tubs.
“What needs to be understood is the vast number of people served by the storehouses,” Noble says. “There are literally hundreds of partners domestically we supply through our storehouses. … The benefit we provide to our partners is that we have a truly robust supply chain. Most nonprofits don’t have the resources to do that, and, with the storehouses, they don’t have to replicate those services. Our storehouse is the warehouse for our partners. They don’t have to worry about paying for storage.”
As much as the materials make a difference in the lives of the families who will receive them, the program also supplies a solution to a business problem for the donors. As manufacturers introduce new items or redesign old ones, they need to do something with older models.
“They don’t want it on the shelves or thrown in the landfill and they don’t want it sold,” Noble explains. “We get it out of the retail system and get it into hands of people who could use it.”
Because the products aren’t being retailed, World Vision releases the manufacturers from their warranties. The organization works with local partners to provide volunteers with the proper training for installation of some products, such as toilets. For other materials, such as water heaters, HVAC systems and blown-in insulation, local contractors handle the installation.
Owens Corning, the world’s largest manufacturer of fiberglass and related products, has been a World Vision corporate partner through the Owens Corning Foundation since 2008. Since 2012, the company has donated enough insulation for nearly 11,000 homes and enough roofing materials for 40 houses.
The insulation alone makes a tremendous impact on the quality of life for a family living in poverty, Noble says. “In Appalachia, almost every home we touch has very poor insulation — or none.”
In 2013, Owens Corning also provided World Vision with a $43,000 grant to purchase two industrial blow-in insulation machines and trailers to transport donated Thermoglas insulation that would have ended up in a landfill.
“World Vision is extremely easy to work with,” says Ann Malak, head of community relations at Owens Corning. “As they have offices and affiliates all over the country, they are able to pick up donations from any of our locations quickly and efficiently. They provide emergency assistance to children and families affected by disasters and conflict in nearly 100 countries. We know our partnership with World Vision is making a difference in communities across the world.”
Reed Slattery manages World Vision’s 20,000-square-foot warehouse in Fife, Wash., near Tacoma. The building materials stored there are available to World Vision’s local partner organizations in need of supplies for construction projects.
“The benefit is huge,” he says. “Sometimes it’s the difference between a project becoming a reality or not getting off the ground.”
The organizations pay a modest handling fee per item that helps World Vision cover its operating expenses.
“One thing I like about the program is that organizations that receive these items will get good-quality materials,” Slattery says. “They don’t have to worry about replacing them for a long time.”
Recently, building materials from the storehouse were used to repair cabins at a church camp and to help a church do repairs at a needy family’s home.
Improvements, such as adding insulation, helps families stay warm and dry during frigid winters in the Pacific Northwest. “We want children to be protected and cared for,” Slattery says. “The building materials program helps a lot with that. Children are living in unsafe conditions, such as freezing cold or mold. Building materials help alleviate that.”
Mission Teams
If you don’t have a working toilet or sink or flooring, it doesn’t foster the growth out of poverty that we are seeking. — Larry Noble, World Vision’s national director for corporate engagementPhilippi, W.V., is the site of World Vision’s Appalachia storehouse. At Philippi, families as well as organizations, can join the storehouse and shop for essential needs and building materials.
Philippi is a popular destination for World Vision short-term mission trips. Church groups are the most common, but individual families are welcome as well. So are college-age and adult groups. Summer trips usually run for a week; on-demand trips in the spring and fall might be for a weekend or a few days. Those are set up individually, says Kris Wamsley, World Vision site program manager for U.S. missions.
The volunteers receive a project information packet ahead of time with details about the community, the family they will be helping and the project they’ll be performing. Housing for the trip might be at a youth camp, a college dorm or at a church. “We try to find places where they can sleep, eat and take a shower all in the same place,” Wamsley says.
Most of the mission teams will do construction-type projects in individuals’ homes. “My little motto is, ‘We like to have these homes safe, warm and dry for the children who are in them,” Wamsley says. “It could be something as simple as painting or maybe putting on a little room addition.”
In addition to using materials that have been donated to the storehouse, groups give a construction donation to purchase the supplies that the storehouse doesn’t have. That way, all the materials the group needs to complete the project are there when they arrive.
Sometimes, volunteers are surprised that there is a need for mission trips in the United States. “When we have new groups, they really get their eyes opened to the poverty here,” she says. “Sometimes it is hard for them to understand about generational poverty. When your grandparents and parents have been in that, it’s a way of life for them.”
People join a mission team for any number of reasons, she says. Many come back year after year because they build relationships with the families they help. “Year after year, they leave a piece of their heart here when they leave,” she says. “That is why a lot of them keep coming back. Their heart is here.”
That’s certainly true for Ralph Cigich, a retired industrial arts teacher and administrator from Murrysville, Pa., who spends up to six weeks a year in West Virginia with World Vision.
“I’ve grown to have so many relationships down there with all the pastors,” he says. “It’s like another family to me there.”
His first project in Appalachia with World Vision was building a foundation for a church. Since then, he’s led groups that have put roofs on houses, installed windows and doors, built porches and handicapped ramps and put in new kitchens. Twice, he has given families the first running water their houses have ever had.
“It’s hard to fathom that people that live that close need that kind of help in the United States,” he says.
The building materials at the storehouse are “just a godsend,” he says. “It’s made a tremendous difference in the lives of these families. Some of them couldn’t afford to go out and purchase materials for their homes. We can use the supplies from the storehouse to make their lives better.”
For more information on a U.S. mission trip or donating building materials to World Vision, contact usprograms@worldvision.org.
Pat Curry is a highly respected journalist who most recently worked as senior editor, sales and marketing, at BUILDER, the official publication of the National Association of Home Builders and the largest-circulation monthly trade magazine in the nation. In 2009, she was named a finalist in the Best Online Article category of the Jesse H. Neal National Business Journalism Awards, the Pulitzer Prize of the trade press.